Лаптев Геннадий Алексеевич – Доцент кафедры автомобильных дорог
и специальных инженерных сооружений ГОУ ВПО «Мордовский
государственный университет им. Н.П. Огарева»,
кандидат технических наук
Введение
Современное строительство немыслимо без бетона. 2 млрд. м3 в год − таков сегодня мировой объем его применения. Последние десятилетия двадцатого века ознаменовались значительными достижениями в технологии бетона. В эти годы появились и получили широкое распространение новые эффективные вяжущие, активные минеральные добавки и наполнители, армирующие волокна, новые технологические приемы и методы получения строительных композитов. Это позволило не только создать и освоить производство новых видов бетона, но и значительно расширить номенклатуру применяемых в строительстве материалов: от суперлегких теплоизоляционных до высокопрочных конструкционных. Сегодня в строительстве применяются более тысячи различных видов бетона, и процесс создания новых бетонов интенсивно продолжается. Это касается, в первую очередь, материалов используемых в конструкциях, работающих в условиях воздействиях высоких температур, динамических нагрузок, ионизирующих излучений.
Необходимо отметить, что быстрое развитие некоторых отраслей промышленности привело к возникновению ряда сложных проблем, связанных с изучением поведения традиционных материалов в ранее не встречавшихся условиях и разработкой специальных материалов со свойствами, более полно отвечающими предъявляемым к ним требованиями.
За последние годы возросло количество технической информации по композиционным материалам. В публикуемых работах имеются ценные сведения о природе этих материалов, рассмотрены физико-химические аспекты поверхностей раздела, изложены особенности структуры и описаны способы их получения. Отмечается способность композитов работать в тяжелых условиях, однако, использование дорогостоящих наполнителей, армирующих элементов и сложность технологии получения ограничивает их применение. Встречается также немало противоречивой информации, требующей анализа и обобщения.
Перспективным направлением дальнейшего развития композитов представляется получение и внедрение эффективных и доступных строительных композитов на металлических связующих – металлобетонов (метонов), обладающих нужными механическими, эксплуатационными и экономическими характеристиками.
1. Исследование диаграммы нагрузка-деформация для металлобетонных плит
Покрытия полов в заводских цехах, как правило, эксплуатируется в тяжелых условиях. Они воспринимают значительные статические и ударные нагрузки, к ним предъявляется повышенные требования по износо- и коррозионной стойкости. Традиционные материалы в недостаточной мере отвечают данным требованиям. Они оказываются либо металлоемкими и дорогостоящими, либо недолговечными.
Разработанные нами металлобетонные плиты на алюминиевом и чугунном связующем имеют ряд преимуществ по сравнению с плитами из традиционных материалов.
Исследования (см. главу 4) показали высокие прочностные характеристики метонов, для подтверждения которых были изготовлены плиты на основе различных материалов с размерами 200×200×15 мм с ребрами жесткости по диагоналям трапецеидальной формы с основаниями 20 и 10 мм, и высотой 15 мм следующихсоставов:
1) из полимербетона состава, в% по объему: эпоксидная смола марки ЭД-20 – 14.9, полиэтиленполиамин -1.64, бутанол – 1.49, маршалит – 14.9, кварцевый песок – 22,35, щебень диабазовый (фракции 7–5 мм) – 44,72;
2) из метона состава, в% по объему: АЛ 2 – 48, щебень базальтовый (фракции 10–7, 7–5 мм), обработанный 3%-ным раствором Н3РО4 – 52;
3) из алюминиевого сплава АЛ 2;
4) из метона состава, в% по объему: чугун серый (СЧ-20) – 40, фарфоровые шарики (диаметром 6 мм) – 60;
5) из метона состава, (в% по объему): чугун серый марки СЧ-20 – 40, фарфоровые шарики (диаметром 10 мм) – 60;
6) из чугуна марки СЧ-20.
Схема испытания плит с опиранием по контуру показана на рис. 1. Результаты механических испытаний плит представлены на рис. 2.

Рис. 2. Зависимость прогибов центра плит от нагрузки: 1 – полимербетон; 2 – AЛ2 – 48% + щебень – 52%; 3 – AЛ2; 4 – СЧ-20 – 40% + фарфоровые шары Ø6 – 60%; 5 – СЧ-20 – 40% + фарфоровые шары Ø10 – 60%; 6 – СЧ-20
Из результатов видно, что нагрузка разрушения метонных плит на основе алюминиевых сплавов в 1,4 раза меньше, при этом модуль упругости в 1,2 раза больше по сравнению с плитами из алюминиевого сплава. Нагрузка разрушения у плит на основе чугуна в 2,2 раза выше, чем у плит с заполнителем из керамических, фарфоровых шариков диаметром6 мм и в 4,4 раза выше плит с заполнителем диаметром10 мм. Модуль упругости у металлобетонных плит с заполнителем в 1,25 раза выше по сравнению с чугунными плитами. При этом участка текучести у плит на основе серого чугуна не наблюдается.
2. Твердость металлобетонов
На твердость испытывались образцы из метона на основе алюминиевого сплава АЛ 2. Испытания образцов производили согласно ГОСТ 9012-99 метонов по методу Бринелля на приборе ТШ-2м, путем вдавливания в образец стального шарика определенного диаметра под действием заданной нагрузки в течение 30 сек. Отношение давления Р к поверхности полученного отпечатка F (шарового сегмента) дает число твердости, обозначаемое НВ.
Рассматривались композиты с дисперсными наполнителями. Дисперсные частицы оказывают упрочняющее действие на композиты в том случае, когда ограничивают деформацию матрицы посредством механического стеснения. Величина упрочнения при этом подчиняется сложной зависимости и является функцией отношения расстояния между частицамик их диаметру, а также отношения упругих характеристик матрицы и частиц. При проведении испытаний в качестве заполнителя использовали кварцевый песок фракции 0,63–1,25 мм, обработанный водным раствором фосфорного ангидрида и борной кислотой, по методике приведенной в 3 гл. Испытание на твердость образцов с более крупным заполнителем не производили, так как в этом случае твердость может быть принята как средняя величина между значениями твердости матрицы и заполнителя.
Образцы в виде плиток толщиной 10 мм изготовлялись с различным содержанием заполнителя методом смешивания расплава с заполнителем и последующим виброуплотнением смеси. Результаты испытания представлены в табл. 1.
Из результатов испытаний видно, что твердость образцов повышается с увеличением степени наполнения и во всех случаях выше твердости чушкового алюминиевого сплава АЛ 2. Наибольшая твердость характерна для составов с содержанием заполнителя – 60%. На твердость композитов влияет обработка поверхности заполнителя. Наблюдается повышение показателя при обработке заполнителя борной кислотой и фосфорным ангидридом на 10–35% по сравнению с контрольными образцами. Одним из факторов повышения твердости композитов на заполнителях, обработанных фосфорным ангидридом, является то, что вокруг частиц заполнителя происходит измельчение зерна и образование фазы тугоплавкого фосфида алюминия (АlР), что и вызвало повышение твердости.
Обработка заполнителя борной кислотой также повлияло на твердость металлобетонных образцов. Произошло сильное измельчение зерна, вызванное тем, что образовались тугоплавкие частицы интерметаллида B2Al и они стали центрами кристаллизации.
3. Истираемость и износостойкость
Металлическая матрица в металлобетонах, с равномерно распределенными в ней частицами заполнителя удерживает в структуре истираемые частицы и принимает на себя различные деформации и нагрузки.
Испытания на истирание проводили согласно ГОСТ 13087-81. Рассматривались составы с заполнителями на основе кварцевого песка, а также керамзита, диабазового, базальтового и гранитного щебня. Составы представлены в табл. 2. Результаты испытаний приведены на рис. 3.

Рис. 3. Истираемость алюминиевых металлобетонов в зависимости от вида заполнителей при длине пути 440 м
Сравнивая результаты испытаний, можно сделать вывод о том, что наименьшая истираемость характерна для составов, в которых в качестве заполнителя использованы горные породы с высокой твердостью. Чем выше твердость заполнителя при пластичной матрице, тем ниже истираемость. Наибольшая истираемость соответствует метону с заполнителем из керамзита. На износостойкость влияет и крупность заполнителя. Более высокую истираемость состава 35 можно объяснить тем, что, выкрашиваясь, песчинки увеличивают абразивный эффект.
Металлобетонные плиты трапецеидального вида размерами 40×35 см с толщиной 4 см прошли производственные испытания на медном руднике (г.Джезказган). Плиты были использованы при облицовке стенок днища бункеров, которые применяются для погрузки медной руды в железнодорожные платформы и отправки ее на горно-металлургический комбинат.
В существующих бункерах плиты облицовки выполняются из марганцовистой стали толщиной 4 см. В процессе эксплуатации стенки и днище бункеров подвергаются сильному абразивному износу в результате удара кусков халькопирита (медного колчедана CuFeS2) и скольжения по плитам облицовки. Обладая высокими показателями плотности – 4,1–4,3 г/см³ и модуля упругости – Е = 8,9·104 МПа халькопирит полностью истирает стальные облицовочные плиты за 6 – 8 месяцев эксплуатации.
Металлобетонные плиты, указанной выше формы, с матрицей из алюми-ниевого сплава АЛ 2 и заполнителями в виде фарфоровых шариков диаметром 10 мм и диабазового щебня, фракции 5–10 мм, вмонтированные в днище бункера, после эксплуатации соответственно в течение 32 и 30 месяцев не имели никаких видимых разрушений.
4. Исследование теплопроводности металлобетонов
Анализ процессов разрушения материалов, вызываемых тепловыми воздействиями, свидетельствует о том, что при оценке свойств конструктивных элементов недостаточно знания таких традиционных механических характеристик, как предел прочности, модуль упругости и т.д. Несущая способность изделий из композиционных материалов в таких условиях определяется также характером и степенью неравномерности температурного поля, и, следовательно, напряженного состояния, которое зависит от теплофизических характеристик компонентов КСМ и условий работы.
Таким образом, исследование термостойкости материалов неразрывно связано с исследованием теплофизических характеристик: тепло- и температуропроводности, т.к. они в этом случае выступают не только как параметры теплопереноса, но и как параметры прочностных критериев.
Теплопроводность композитов в общем случае определяется теплопроводностью составляющих компонентов, их соотношением, типом структуры, видом поверхности раздела и существенно зависит от размеров заполнителя.
Теплопроводность метонов с матрицей из алюминиевого сплава АЛ 2, серого чугуна СЧ-20 и конструкционного алюминиевого чугуна (КАЧ) определяли на установке, показанной на рис. 4. Изготовленные образцы имели форму цилиндра с диаметром основания 30 и высотой 300 мм.
Если объемная концентрация одной из компонент не превышает 0,2, то расчет теплопроводности проводили по формуле:

Рис. 4. Схема прибора для определения теплопроводности: 1 – водяной охладитель; 2 – асбестоцементный корпус; 3 – образец; 4, 6 – огнеупорные уплотнители; 5 – электронагреватель; 7 – сосуд Дьюара; T1 – T5 – термопары; Г1 – Г5 – гальванометры; А – амперметр; V – вольтметр; R – реостат
Экспериментальных работ по определению теплопроводности композиционных материалов на металлических связующих крайне мало, поэтому использование моделей и методов обобщенной теории проводимости для оценки и проектирования таких материалов с требуемыми свойствами представляется вполне целесообразным. Для определения теплопроводности нужно знать: количество теплоты, отдаваемое образцом при стационарном режиме через его поверхность (q); температуру нагреваемого конца стержня (Т1); температуру в какой-либо точке образца на расстоянии Х от нагреваемого конца (ТХ); площадь поперечного сечения образца (S); температуру окружающей среды (Т0). Тепло, отдаваемое, электропечью Q = 0,24 × J0V0 расходуется на нагрев окружающей среды и образца. При выведении образца из печи количество теплоты, идущее на нагрев окружающей среды, определяется при ее нагреве до температуры ТХ. Отсюда, теплота, идущая на нагрев образца, определяется из выражения:
Q = Q0 – Q1 = 0,24 (J0V0 – J1V1). (4)
Измерения коэффициента теплопроводности λ производят после того, как установится тепловое равновесие, т.е. показания гальванометра остановятся на определяемых значениях температуры. Коэффициент теплопроводности композита определяется по формуле:
λ = q·x / [S (T1 – T0] ln ((T1 – T0) / (TX – T0))]. (5)
Для проверки экспериментальных данных расчет теплопроводности производили по формулам Эйкена-Оделевского (1) и (2). Расчеты выполнялись на персональном компьютере. Значения теплопроводности для композиций с наполнителем из диабаза, базальта, габбро, фарфора и матрицей из алюминиевого сплава АЛ2, серого чугуна, конструкционного алюминиевого чугуна приведены в табл. 3.
Результаты исследований были обработаны с использованием методов математического планирования эксперимента. В качестве варьируемых факторов рассматривались: Х1 – коэффициент теплопроводности заполнителя; Х2 – объемная доля матрицы. Матрицами служили алюминиевый сплав марки АЛ2, серый чугун марки СЧ-20 и алюминиевый конструкционный чугун марки КАЧ. Рассматривались варианты расчетов при нормальной температуре, а также при 60, 100 и 500ºС. Коэффициенты теплопроводности в зависимости от условий испытаний равны: алюминиевого сплава – 140 Вт/мºК (при t = 18 – 20ºС); серого чугуна – 54,6 Вт/мºК (при t = 60ºС); серого чугуна – 44,1 Вт/мºК (при t = 510ºС); алюминиевого конструкционного чугуна – 84,0 Вт/мºК (при t = 100ºС); алюминиевого конструкционного чугуна – 420 Вт/мºК (при t = 500ºС). После обработки результатов эксперимента получено уравнение регрессии в виде модели следующего вида:
Y=b0+b1·X1+b2·X2+b11·X12+b12·X1X2+b22·X22+b111·X13+b112·X12X2+
+b122·X1X22+b222·X23+b1112·X13X2+b1122·X12X22+b1222·X1X23 (6)
По уравнениям регрессии построены графические зависимости (рис. 5–9).

Рис. 5. Зависимость изменения теплопроводности металлобетонов с матрицей АЛ 2 от объемной доли заполнителей

Рис. 6. Зависимость изменения теплопроводности металлобетонов с матрицей СЧ-20 при 60°С от объемной доли заполнителей
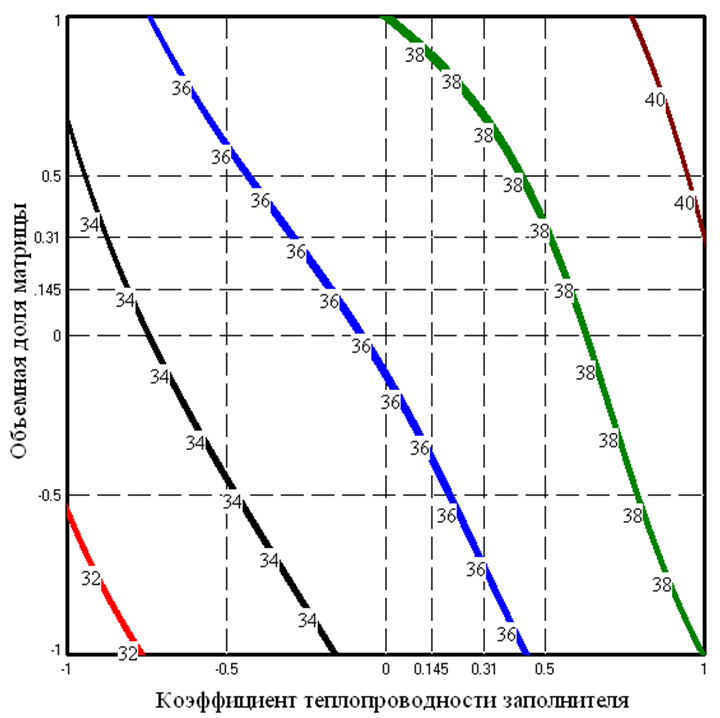
Рис. 7. Зависимость изменения теплопроводности металлобетонов с матрицей СЧ-20 при 510°С от объемной доли заполнителей

Рис. 8. Зависимость изменения теплопроводности металлобетонов с матрицей из конструкционного алюминиевого чугуна при 100°С от объемной доли заполнителей

Рис. 9. Зависимость изменения теплопроводности металлобетонов с матрицей из конструкционного алюминиевого чугуна от объема доли заполнителей
Основываясь на анализе графических зависимостей можно сделать следующие выводы:
При использовании в качестве матрицы сплава марки АЛ 2 (λ2 = 140 Вт/м · ºК), а в качестве заполнителя фарфоровых шариков (λ1 = 1,4 Вт/м · ºК ), коэффициент теплопроводности снижается на 35%по сравнению с чистым сплавом АЛ 2. Применяя в качестве заполнителей другие материалы с более низкой теплопроводностью и выполняя их поверхностную обработку, можно значительно снизить теплопроводность композита в целом. Сравнивая результаты экспериментальных данных (λСР = 91,6 Вт/м · ºК) с расчетными (λСР = 89,418 Вт/м · ºК, m2 = 0,3), можно сделать вывод, что формулой можно пользоваться при расчете теплопроводности метонов при различных соотношениях компонентов и с различными заполнителями.
5. Исследование температуропроводности металлобетонов
Испытания на температуропроводность металлобетона проводились на образцах размерами 40×40×160 мм по схеме, показанной на рис. 10. В качестве регистрирующего прибора использован шестиканальный самопищущий электронный потенциометр типа КСП-4 ГОСТ 7164-71 (1). Датчиками температуры служили пять хромель-алюмелевых термопар (2), которые закреплялись на ровном расстоянии друг от друга (40 мм) по длине на поверхности образца (3). Источником тепла служил стандартный бытовой электронагреватель ГОСТ 306-69 (4) с температурным интервалом 20–450ºС и мощностью 600 Вт. Для уменьшения искажений в показаниях первой от нагревателя термопары и обеспечения надежного теплового контакта всей торцевой поверхности образца с нагревателем использовалась ванна с расплавом олова (5). Термопары были соединены с потенциометром, экранированным многожильным кабелем (6).
Результаты испытаний обобщены на графиках (рис. 11–14). На рис. 11 представлена наиболее характерная диаграмма изменения температуры поверхности образца в координатах «температура – время».

Рис. 10. Схема температурных испытаний металлобетонных образцов: 1 – потенциометр КСП-4; 2 – хромель-алюмелевые термопары; 3 – металлобетонный образец; 4 – электронагреватель; 5 – ванна с расплавом олова; 6 – многожильный кабель
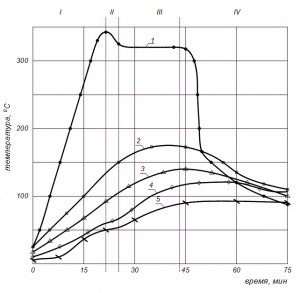
Рис. 11. Диаграмма изменения температуры поверхности метонных образцов с матрицей из серого чугуна на термопарах, установленных согласно рис. 10: 1 – график показаний термопары I; 2 – то же для II; 3 – то же для III; 4 – то же для IV; 5 – то же для V
Кривые (1–5) на графике соответствуют показаниям термопар (I–V) и отображают процесс изменения температуры поверхности образца в течение всего цикла испытания: от начала прогрева до достижения образцом при охлаждении температур порядка 100°C. Образцы охлаждались равномерно и одновременно, т.к. показания термопар во всех точках практически совпадают (разница в показаниях составляет 3–5°С). Каждый цикл испытаний был разделен на три этапа, что нашло свое отражение и на графиках: участок I соответствует этапу равномерного повышения температуры нагревателя; участок III – этапу поддержания температуры на одном уровне; участок 1V – этапу охлаждения образца на воздухе (участок II – переходный этап стабилизации температурного режима нагревателя). Рассмотрим диаграмму по участкам:
I участок. На данном этапе эксперимента температура нагревателя возрастала с практически постоянной и сравнительно высокой скоростью, до 16°С/мин (кривая 1). В то же время скорость подъема температуры на следующих участках образца гораздо ниже, особенно – на первом, что говорит о довольно низкой температуропроводности метона, главным образом в районе нагрева; так, в конце участка разность показаний термопар I и II достигает (340 – 130) = 210°С. Разность показаний остальных термопар меньше, причем каждая следующая меньше предыдущей, что наглядно показывают расстояния между кривыми 2–3, 3–4, 4–5. Общая разность температур между термопарами I и V достигает (340°С – 50°С) = 290°С.
Для выявления закономерности распространения температуры по длине образца на данном этапе циклов испытаний был построен график температурных полей по длине образца в фиксированные промежутки времени (рис. 12).

Рис. 12. Изменение температуры по длине образца во времени в местах установки термопар (I, II, III, IV, V – номера термопар) при возрастании температуры нагревателя (τ = 2,1 мин.)
В координатах “температура-удаление от источника нагрева (длина образца)” были построены кривые, все точки которых были зафиксированы практически одновременно (температурные изохромы). Интервал времени между кривыми – 2,1 мин. Форма кривых (особенно – I, II, III) приближается к экспоненциальной. Кроме того, на участке 1 графика (рис. 11) отчетливо прослеживается большая инерционность в распространении температуры; особенно – на кривой V, достигающая в начале участка 8 мин.
Участок II из рассмотрения исключается ввиду его нехарактерности (в некоторых циклах он имел плавный переход, без пика) и кратковременности (не более 2–3 мин.).
На участке III также наблюдается резкий спад температуры между термопарами Iи II (170°С в начале и 145°С в конце участка). Общая разность температур (между термопарами I и V) составляет соответственно 275 и 230°С. Как и для участка I, был построен изохронный график температурных полей по длине образца (рис. 13), который подтвердил экспоненциальный характер распространения температуры в метоне на основе чугуна.

Рис. 13. Изменение температуры по длине образца во времени в местах установки термопар (I, II, III, IV, V – номера термопар) при постоянной температуре нагревателя
Инерционность в распространении температуры также подтверждается: максимум показаний термопары II достигается лишь к концу участка; а более удаленных термопар III,IV, V – на участке IV.
Участок IV диаграммы соответствует этапам охлаждения образца на воздухе и характеризуется резким снижением показаний термопары Iв начале участка и более пологим после приближения к показаниям остальных термопар. Скорость охлаждения на остальных участках образца – более равномерная и к концу участка показания всех термопар почти выравниваются. Изохронные поля температур (график на рис. 14) также имеют сходящуюся форму.
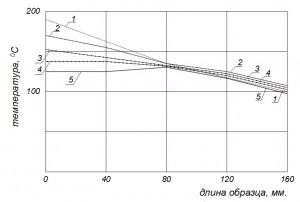
Рис. 14. Изменение температуры по длине образца во времени в местах установки термопар (I, II, III, IV, V – номера термопар) при снижении температуры нагревателя
Заключение
Таким образом, экспериментальными исследованиями установлено, что при введении заполнителя повышается твердость композитов, за счет ограничения деформации матрицы посредствомее механического стеснения. Испытания на истирание показали высокую износостойкость метона, которая достигается совместной работой пластичной матрицы, принимающей на себя различные деформации и твердого износостойкого заполнителя. При этом установлено, что износостойкость пропорциональна твердости заполнителя, зависит от его крупности и адгезии на границе контакта «металл – заполнитель». Выявлено, что теплопроводность метонов зависит от вида матрицы и заполнителя, обратно пропорциональна количеству заполнителя и снижается на 30-35%по сравнению с чистыми металлами. При этом скорость распространения температуры в метоне меньше, чем в металлах и носит спадающий характер при удалении от источника нагрева. Испытания плит на основе металлобетонов показали, что они обладают более высокими механическими и эксплуатационными характеристиками по сравнению с плитами, полученными с применением традиционных материалов – бетона, железобетона и полимербетона.